INTRODUCTION
Au cours de notre stage ouvrier en STH, nous avons été amenés à utiliser divers outils pour réaliser des opérations mécaniques. Parmi eux, la clé à cliquet a retenu notre attention pour une potentielle optimisation, visant à améliorer son ergonomie et à accroître l'efficacité du travail. Un des inconvénients de cet outil est la nécessité de changer de douille à chaque variation de taille de boulons par exemple. Nous avons donc imaginé un concept de douille ajustable, capable de s'adapter à différentes tailles, permettant ainsi à l'utilisateur de n'avoir qu'une seule douille pour travailler sur plusieurs dimensions.
1. ANALYSE FONCTIONNELLE
1.1 Analyse du besoin
1.1.1 Identifier le besoin
- Faciliter les travaux de mécanique en réduisant le nombre d'outils nécessaires.
- Accélérer les opérations grâce à un mécanisme adaptable.
- Agir sur la variabilité des tailles d'écrous et de boulons.

Figure 1 : Bête à cornes représentant le besoin
1.1.2 Validation du besoin
Pourquoi une douille à taille variable ?
- Gain de temps : Lors de travaux de mécanique ou de bricolage, changer constamment de douille en fonction de la taille des écrous ou boulons peut être fastidieux et chronophage. Une douille à taille variable permet de passer rapidement d'une taille à l'autre sans interrompre le flux de travail.
- Réduction du nombre d'outils : Les kits de douilles traditionnels nécessitent un grand nombre de tailles différentes. Une douille à taille variable réduit considérablement la quantité d'outils à transporter.
- Encombrement et poids réduits : Moins d'outils signifie moins de poids et d'espace occupé dans la boîte à outils.
- Polyvalence : Certains travaux nécessitent de jongler entre plusieurs tailles de fixations. Une douille à taille variable permet de répondre à une plus grande variété de situations avec un seul outil.
Qu'est-ce qui pourrait la faire évoluer ou disparaître ?
- Échec à répondre aux exigences de robustesse : Si la douille à taille variable s’avère moins durable que les douilles traditionnelles lors d'un usage intensif, les utilisateurs pourraient revenir aux douilles standard, plus fiables.
- Obsolescence des écrous et boulons standards : L'évolution des techniques d'assemblage. Par exemple, avec des systèmes de fixation sans boulons, des attaches rapides ou d'autres solutions innovantes.
1.2. Recherche sur les interactions avec l'environnement extérieur
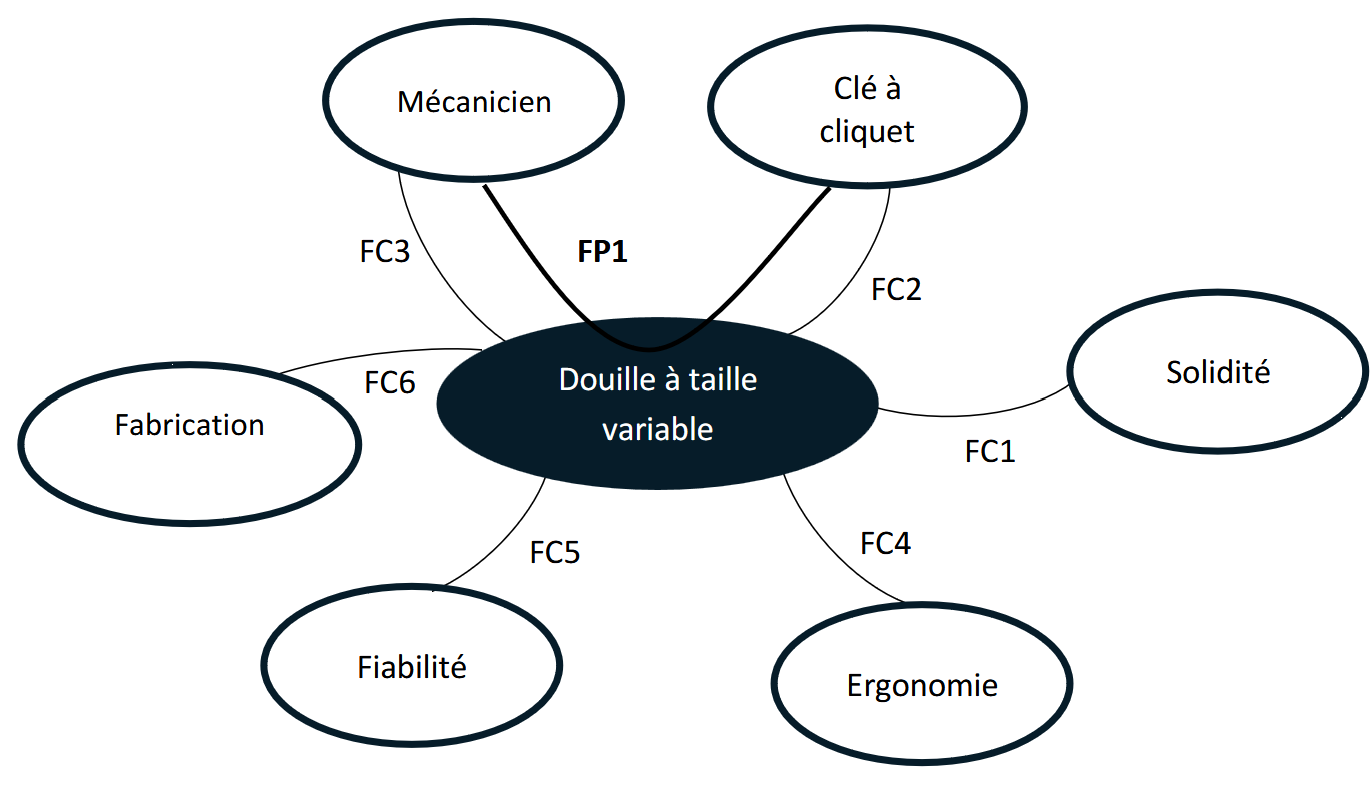
Figure 2 : Diagramme d'analyse des besoins
FP1 : Permet le serrage de boulons/vis de différentes tailles avec une seule douille
FC1 : La douille doit être suffisamment robuste pour résister aux efforts mécaniques.
FC2 : La douille doit être adaptée aux cliquets standards.
FC3 : Elle doit être facile à manipuler.
FC4 : La douille doit être confortable à utiliser.
FC5 : Elle doit fonctionner sans défaillances et être durable.
FC6 : La douille doit être réalisable avec des processus de fabrication adéquats (FabLab).
2. ÉTAT DE L'ART
Analyse des solutions actuelles
À la suite de cette analyse, nous avons étudié toutes les solutions existantes pour nous assurer que notre prototype n’est pas déjà disponible sur le marché. Nous avons également évalué leurs limites et compris comment nous pouvions proposer une nouvelle solution innovante dans cette démarche d’optimisation produit. Nous avons donc rassemblé dans un tableau récapitulatif tous les dispositifs existants :

Figure 3 : Tableau solutions existantes
3. CAHIER DES CHARGES FONCTIONNEL
Grâce à notre étude des solutions existantes ainsi que leurs limites, nous avons pu déterminer quels étaient les critères qu’allait devoir respecter notre prototype. Un cahier des charges a été élaboré en premier lieu, basé sur les critères d’une douille ajustable souhaitée. Cependant, comme ce projet est encore en phase de recherche, il pourrait évoluer une fois qu’un concept sera validé. Certains critères n’ont pas encore été déterminés et nous ne voulons pas nous limiter d’emblée. Pour innover, il est souvent essentiel d’adopter des approches moins conventionnelles.

Figure 4 : Cahier des charges fonctionnel
4. PROPOSITIONS TECHNIQUES
4.1 Principes explorés
4.1.1 Solution avec ressort en compression extérieure
Le principe de fonctionnement de cette 1ère solution est de tourner une molette afin de translater radialement 6 mâchoires qui épousent alors la forme et la taille du boulon à serrer. Plus précisément, la rotation de la mollette entraîne une vis sans fin en rotation, elle-même entrainant en translation une pièce venant en butée sur les 6 mâchoires afin de les écarter. Les mâchoires sont chacune maintenues vers le centre par 6 ressorts placés radialement entre chaque mâchoire et le support extérieur. Ainsi, l’utilisateur est capable d’écarter ou de resserrer les mâchoires en tournant simplement une molette.
L’avantage de cette solution est la possibilité d’actionner le mécanisme à une seule main.
Les inconvénients sont d’une part le nombre de pièces en mouvement : 1 rotation entrainant une translation entrainant 6 autres translations ; et d’autres part, l’utilisation de ressorts qui risquent de complexifier le mécanisme : durée de vie, raideur précise à déterminer, limite du nombre de taille utilisable.

Figure 5 : Schéma solution 1

Figure 6 : Modélisation solution 1
4.1.2 Solution avec ressort en compression intérieure
Le principe de fonctionnement de cette deuxième solution est de tourner la pièce supérieure extérieure afin de translater radialement 6 mâchoires qui épousent alors la forme et la taille du boulon à serrer. Plus précisément, la pièce supérieure extérieure est en liaison hélicoïdale par rapport au support ; sa rotation va donc la translater. Cette pièce supérieure est également en appui plan par rapport aux 6 mâchoires qui sont construites de façon à se resserrer lorsque la pièce extérieure descend. Les 6 mâchoires sont chacune maintenues en butée contre la pièce supérieure extérieure par 6 ressorts placés radialement entre chaque mâchoire et un axe central. Ainsi, l’utilisateur est capable d’écarter ou de resserrer les mâchoires en tournant simplement une pièce.
Il y a moins de pièces en mouvement par rapport à la première solution.
Le principal inconvénient est l’utilisation de ressorts qui risquent de complexifier le mécanisme : durée de vie, raideur précise à déterminer, limite du nombre de taille utilisable.

Figure 7 : Schéma solution 2

Figure 8 : Modélisation solution 2
4.1.3 Solution avec ressort spirale d'entraînement
Cette solution s’inspire du fonctionnement d’un mandrin de perceuse. Son principe repose sur la rotation d’une pièce extérieure supérieure dotée d’une empreinte en spirale. En tournant cette pièce, la spirale, qui est en liaison rainure avec 6 mâchoires, provoque leur translation radiale. Ces mâchoires s’ajustent ainsi à la forme et à la taille du boulon à serrer. Plus précisément, les mâchoires sont également en liaison glissière avec le bâti, ce qui permet à leur mouvement radial d’être guidé par la rotation de la spirale. L’utilisateur peut alors écarter ou resserrer les mâchoires en actionnant simplement une pièce accessible et facile à manipuler.
Cette solution présente plusieurs avantages. D’une part, elle réduit le nombre de pièces en mouvement par rapport aux deux premières options. D’autre part, elle maximise la plage de tailles des boulons compatibles, car aucun ressort ne limite cette caractéristique. De plus, l’absence de ressorts élimine le risque de fatigue de ces composants, augmentant ainsi la durabilité du produit.
Cependant, le principal inconvénient réside dans la complexité de la spirale, qui peut engendrer un jeu avec les mâchoires.
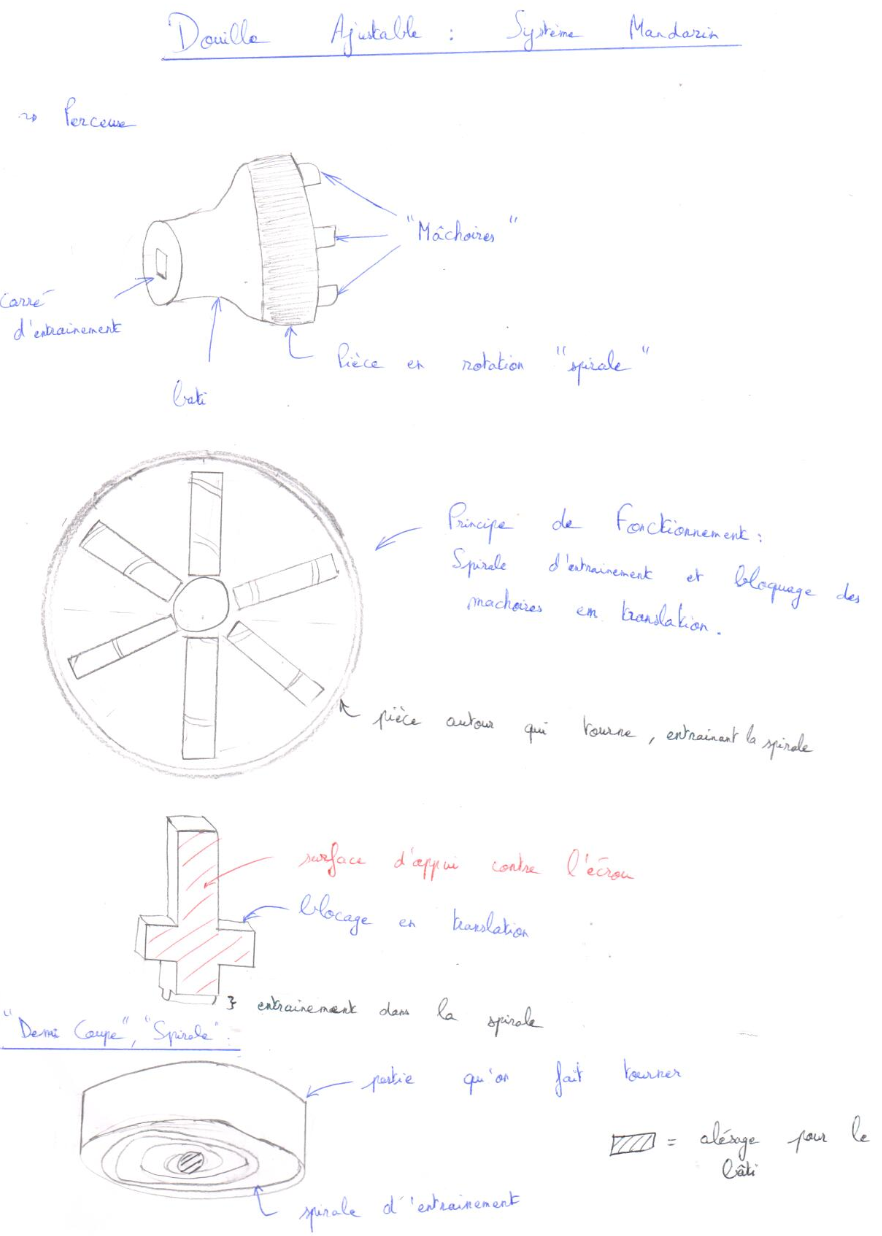
Figure 9 : Schéma solution 3

Figure 10 : Modélisation solution 3
4.2 Solution envisagée
Nous avons fait le choix de retenir le modèle avec spirale, car il nous a semblé le plus optimisé. En effet, le nombre de pièces en mouvement est limité au maximum tout en proposant une plage de taille la plus grande possible, l’objectif principal de notre cahier des charges. Cette solution ne présente pas non plus de ressort, ce qui simplifie le mécanisme et donc sa faisabilité.
5. CONCEPTION
5.1 Principe et concept de la spirale d'Archimède
La spirale utilisée pour déplacer les mâchoires est une spirale d’Archimède, qui se caractérise par une équation mathématique simple où le rayon augmente proportionnellement à l’angle de rotation. Ce type de spirale est idéal pour générer un mouvement linéaire continu dans les systèmes mécaniques tout en permettant un guidage précis des éléments associés. L’expression générale en coordonnées polaires est donnée par :
Où : r est le rayon à un angle donné, θ est l’angle polaire (en radians ou degrés), a est le rayon initial (constant), b est le coefficient d’augmentation du rayon par unité d’angle.
Sous CREO, la spirale a été définie en coordonnées cylindriques avec les équations suivantes :
𝜃 = 3 × 360 × 𝑡
𝑦 = 0, 𝑥 = 𝑟 × cos(𝜃) , 𝑧 = 𝑟 × sin(𝜃)
Ces équations traduisent le déplacement radial et angulaire de la spirale en fonction du paramètre t, qui varie de 0 à 1 pour parcourir l'ensemble des tailles de douilles.
- Rayon initial r = 8 mm : Ce rayon de départ a été choisi pour que la première taille de douille soit de 12 mm. Le décalage entre la surface de la mâchoire en contact avec l’écrou et le guide de la mâchoire, situé dans la rainure de la spirale, nécessite un ajustement initial du rayon.
- Progression radiale 14⋅t : La progression radiale permet de couvrir la plage de tailles de 12 mm à 28 mm. Le choix de cette valeur tient compte de la contrainte d'un nombre limité de tours (moins de 2 tours effectifs) tout en garantissant un déplacement précis des mâchoires.
- Rotation angulaire θ = 3⋅360⋅t : Cette rotation de 3 tours permet un verrouillage mécanique à la fin du mouvement, tout en respectant la contrainte de rotation effective de deux tours pour couvrir la plage de tailles. Ce tour supplémentaire offre une marge pour le blocage physique des mâchoires au bout de la spirale.
Le profil de la spirale est légèrement incliné pour assurer un glissement fluide des mâchoires. L'angle d'inclinaison a été ajusté au cours des itérations en impression 3D (voir section Fabrication).

Figure 11 : Courbe d’Archimède modélisée

Figure 12 : Balayage du profil de la spirale
5.2 Guidage des éléments mécaniques
Nous avons ajouté une bague extérieure autour de la spirale, permettant à l’utilisateur de la manipuler
facilement. Cette bague est libre en rotation autour de son axe, mais bloquée en translation grâce à sa fixation
entre la glissière et le bâti.
Les mâchoires, quant à elles, sont guidées par la spirale et maintenues en position par la glissière. Elles
constituent une pièce essentielle de l’assemblage, car elles assurent la fiabilité de la douille lors des réglages de
position. Pour limiter le phénomène de rotulage des mâchoires dans la glissière, nous avons ajouté des
épaulements en haut et en bas des mâchoires. Ces épaulements s’appuient respectivement sur les parties
supérieure et inférieure de la glissière, dont la largeur a été augmentée afin de réduire ce jeu.

Figure 13 : Liaison glissère entre le bâti et les mâchoires
Un décalage entre les six mâchoires a été introduit pour assurer un déplacement uniforme, toutes restant équidistantes du centre de la douille. Ce décalage, lié au guidage des mâchoires le long de la spirale, compense la rotation de celle-ci. Chaque guide de mâchoire est ainsi décalé de 0.8 mm par rapport au précédent.

Figure 14 : Décalage des guides de mâchoires observé dans l'assemblage
Enfin, pour renforcer la solidité globale entre le bâti, la glissière et l’arbre central qui maintient l’ensemble, nous avons choisi de diviser ces trois composants. Cela nous permet de les assembler par collage, réduisant ainsi les faiblesses potentielles dues à l’orientation des couches dans l’impression 3D, particulièrement dans les zones d’intersection.
5.3 Carré de manœuvre
Notre douille à taille variable, comme toutes les douilles disponibles sur le marché, est équipée d’un carré de manœuvre permettant sa fixation sur une clé à cliquet. Sa conception s’appuie sur la norme NF ISO 1174-1, qui définit les dimensions des carrés de 1/2". En respectant ces spécifications, nous avons obtenu un carré femelle standardisé, compatible avec toutes les clés à cliquet couramment utilisées.

Figure 15 : Carré de manœuvre conforme à la norme NF ISO 1174-1
5.4 Ressort à bille de position
Selon le cahier des charges, il était nécessaire d'intégrer un indicateur permettant de déterminer si l’on se trouve dans une position correspondant à une taille spécifique. L'objectif était de faciliter le positionnement des mâchoires pour une taille donnée. Nous avons envisagé plusieurs solutions, notamment l’ajout d’une graduation sur la bague extérieure, mais c’est l’utilisation d’un poussoir à bille de position qui a retenu notre attention. Couramment employé dans le domaine de l’horlogerie, ce mécanisme permet de ressentir un clic lors de la mise en position et offre une légère résistance pour stabiliser cette dernière.

Figure 16 : Ressorts à billes de position
Dans notre cas, nous avons choisi d’intégrer ces poussoirs directement dans les mâchoires. En effet, l’angle associé au changement de taille n’étant pas uniforme, il n’était pas possible de les placer sur la bague extérieure. Nous avons donc inséré un poussoir à bille entre les mâchoires et la spirale, logé dans l’épaisseur même des mâchoires. Par ailleurs, nous en avons installé dans les six mâchoires afin que les positions soient suffisamment espacées pour éviter un resserrement excessif entre elles.

Figure 17 : Intégration des ressorts à billes de position directement dans les mâchoires
5.5 Moletage
Dans une optique ergonomique, nous avons intégré un effet de moletage sur la bague extérieure pour améliorer la prise en main et faciliter la manipulation de la douille. Ce motif a été conçu en combinant les fonctions de balayage et de répétition linéaire, permettant ainsi de reproduire un profil similaire à un moletage usiné.

Figure 18 : Moletage 3D créé par projection et répétition de géométries
6. VALIDATION ET SIMULATION
6.1 Choix des matériaux
La douille subit de fortes contraintes lors de son utilisation. C’est pourquoi nous avons porté une attention particulière au choix des matériaux pour garantir sa résistance. Ce choix a été influencé par des critères pratiques et techniques, notamment la compatibilité avec les méthodes de fabrication utilisées, à savoir l’impression 3D et la découpe à jet d’eau.
La machine de découpe jet d’eau, limitée à des pièces planes en 2D, a été utilisée pour fabriquer la partie centrale des mâchoires en acier. Ce matériau a été choisi pour sa solidité et sa résistance à l’usure, car cette pièce entre directement en contact avec l’écrou à visser et doit supporter des contraintes importantes. La mâchoire est composée de trois parties : une pièce centrale en acier découpée à la jet d’eau, et deux pièces imprimées en 3D qui s’assemblent de chaque côté. Cette configuration permet de guider les mâchoires dans la glissière tout en garantissant leur solidité. La partie de la mâchoire qui est guidée par la spirale fait partie de la même pièce en acier. Cela permet d'assurer un mouvement précis de la mâchoire et d'éviter tout risque de casse au niveau de la tête de guidage dans la spirale.
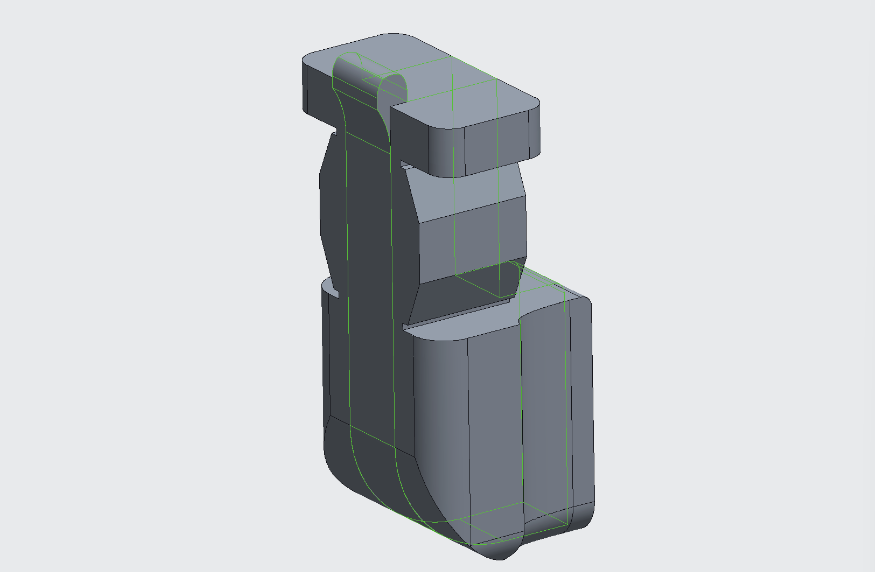
Figure 19 : Division de la machoire, le renfort en acier étant au milieu
Pour toutes les autres pièces, nous avons choisi l'impression 3D comme méthode de fabrication car la forme de ces pièces est complexe et nécessite une bonne qualité pour que le mécanisme fonctionne correctement. Pour choisir le matériau adapté pour l'impression 3D, nous avons étudié les matériaux disponibles au FabLab. Nous avons besoin d'un matériau avec une limite élastique élevée pour éviter que la pièce ne se déforme plastiquement, ce qui pourrait empêcher le bon fonctionnement du mécanisme. Il est également essentiel d'avoir un module de Young élevé afin de limiter les déformations élastiques, garantissant ainsi que la pièce ne subisse pas de déformation excessive lors de son utilisation. Bien que la méthode d'impression 3D limite nos choix de matériaux, nous avons tout de même cherché à optimiser la solidité avec les ressources disponibles. Pour cela, nous avons utilisé CES EduPack pour classer les matériaux en fonction de leur limite élastique et de leur module de Young. Les matériaux les plus adaptés apparaissent dans le quart supérieur droit du diagramme.

Figure 20 : Classement des matériaux avec CES EduPack
Dans notre cas, bien que ces propriétés soient importantes pour évaluer la résistance mécanique des matériaux, il est essentiel de prendre en compte d’autres critères, comme la ductilité notamment, qui permet d’éviter une rupture brutale sous contrainte. Par exemple, le PA (Polyamide) et son dérivé PA-CF (renforcé en fibre de carbone), présentent une meilleure ductilité que l’ABS et le PLA, ce qui les rend plus résistants aux impacts et aux charges dynamiques. Le PA-CF, en particulier, offre des performances mécaniques supérieures à l'ABS, tout en étant plus économique que le PEEK, qui, bien que très performant, reste plus coûteux. En tenant compte de ces facteurs, le PA-CF, disponible au FabLab, a été choisi pour son excellent compromis entre résistance mécanique, durabilité, et coût.
6.2 Simulation
La simulation par analyse par éléments finis (FEA) a été un outil clé dans le développement de notre
douille. Cette approche a permis de simuler les contraintes, déformations et zones critiques sous
différentes charges et conditions d’utilisation. En particulier, cette analyse a joué un rôle crucial dans
le choix des matériaux, en identifiant ceux qui offrent le meilleur compromis entre résistance
mécanique et durabilité.
Nous avons souhaité réaliser une simulation des contraintes sur l’assemblage complet pour évaluer sa
résistance, mais en raison de la complexité du mécanisme, nous n’avons pas pu contraindre certains
mouvements tels que celui des mâchoires dans la spirale et la glissière. Nous nous sommes donc
concentrés sur des simulations analysant uniquement une partie de la douille.
Pour la simulation, nous avons isolé l’arbre et la glissière, les deux composants subissant les contraintes
les plus élevées. Nous avons en effet négligé la déformation des mâchoires car elles sont fabriquées
en acier, et leur déformation par rapport aux autres composants imprimés en 3D est donc négligeable.
De même, comme l’arbre est collé au bâti, nous avons ignoré la présence du bâti dans la simulation.
En fait, nous avons traité l’arbre et la glissière comme une seule pièce pour la simulation, car ils sont
collés ensemble et forment une liaison rigide. Ensuite, nous avons divisé les faces de cette pièce afin
de paramétrer les charges. Concrètement, nous avons isolé la partie de l’arbre qui reste rigide par
rapport au bâti et appliqué un couple dans le sens de serrage d’un écrou. Pour la glissière, nous avons
isolé les faces correspondant à l’appui d’une mâchoire lors du serrage d’un boulon, fixant tous les
degrés de liberté de ces surfaces. Nous avons effectué les simulations pour la taille qui génère la
contrainte maximale (la taille de la douille maximale, soit 28 mm dans notre cas). Ainsi, nous analysons
la déformation de la glissière et de l’arbre en torsion lors d’un serrage.

Figure 21 : Analyse déformation arbre + glissière en torsion
Nous avons cherché à déterminer, grâce à la simulation, le couple maximal que la douille peut supporter avant déformation plastique. Pour cela, nous avons calculé la contrainte maximale admissible correspondant à la limite élastique d’un certain matériau avec un coefficient de sécurité de 1,5. Par exemple, pour l’acier S355, on obtient σadm = σe/S = 355/1,5 ≈ 236,67 MPa. Soit une contrainte maximale admissible de 236,67 MPa à ne pas dépasser en simulation en comparant cette valeur au résultat obtenu pour la contrainte de Von Mises.
6.3 Validation
Cette démarche nous a permis de comparer différentes options de matériaux et de valider le choix du
matériau retenu. Pour certains matériaux, comme le PA-CF (non inclus par défaut dans CREO Simulate),
nous avons dû créer un matériau personnalisé dans la bibliothèque de CREO Simulate en nous basant
sur les données fournies dans la fiche technique du fabricant. En suivant le protocole décrit dans la
section précédente, nous avons obtenu et visualisé les résultats de contrainte et de déplacement.
Concernant la simulation du PA-CF, les résultats obtenus sur CREO Simulate sont présentés ci-après.

Figure 22 : Résultats obtenus avec Creo Simulate
À partir des données collectées pour l’ensemble des matériaux, nous avons regroupé toutes les simulations dans le tableau suivant.

Figure 23 : Données regroupées pour les différents matériaux
Le PA-CF offre un bon compromis entre solidité, prix et facilité d’impression, matériau que nous avons donc retenu pour les pièces imprimées en 3D. Nous avons également testé des matériaux plus solides, comme l'acier et le laiton, même s'ils ne sont pas adaptés à l'impression 3D. L'idée était de voir ce que cela donnerait avec des procédés de fabrication plus lourds, comme le moulage ou l’usinage. Les résultats obtenus sont convaincants par rapport aux objectifs fixés pour la douille.
7. FABRICATION
7.1 Choix des méthodes de fabrication et mise en œuvre
7.1.1 Découpe jet d’eau
Les renforts en acier des mâchoires ont été réalisés à partir d’une chute de plaque d’acier S355, un choix pertinent compte tenu du contexte. Pour usiner ces pièces, nous avons opté pour une découpe à jet d’eau, une méthode adaptée à la coupe de profils 2D dans des plaques métalliques. La plaque utilisée avait une épaisseur correspondant directement à celle des renforts requis, évitant ainsi des étapes de reprise d’usinage. Le profil 2D de ces renforts a été exporté au format DXF depuis CREO. Par la suite, le fichier DXF a été converti en G-code, le langage machine utilisé par la machine de découpe jet d’eau Wazer du FabLab, à partir du logiciel Wazercam. Cette machine s’est avérée idéale pour réaliser des découpes précises dans le S355, évitant toute déformation thermique souvent rencontrée avec d’autres techniques comme la découpe laser ou plasma. En complément, nous avons porté une attention particulière à la qualité de finition des pièces, en éliminant les bavures potentielles après découpe et en vérifiant les cotes pour garantir un assemblage optimal avec les composants en plastique. En particulier, les trous destinés aux ressorts à bille, trop petits pour être usinés avec précision par découpe jet d’eau, n’avaient pas les dimensions correctes après cette opération. Un second passage à la perceuse à colonne a donc été nécessaire pour finaliser leur usinage.
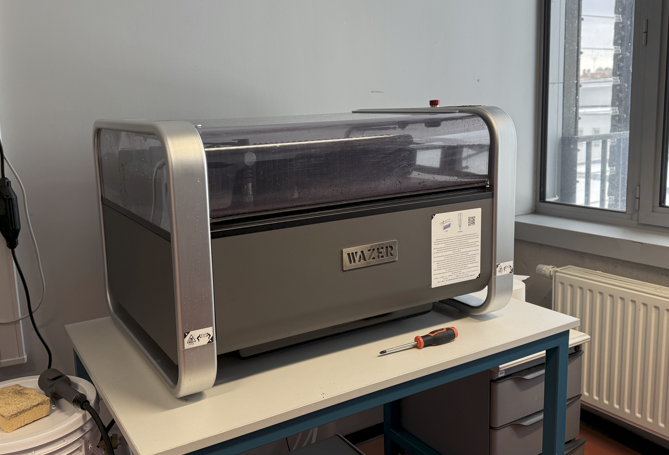
Figure 24 : Découpe jet d'eau WAZER du Fab Lab

Figure 25 : Découpe de notre plaque d'acier S355
7.1.2 Impression 3D
Pour les parties plastiques de la douille, nous avons choisi un matériau technique : le PA-CF. La fabrication a été réalisée à l’aide d’imprimantes 3D FDM (Fused Deposition Modeling), en particulier le modèle Bambu Lab X1C, qui est idéal pour l’impression de matériaux techniques. Cette imprimante dispose d’une chambre d’impression chauffée, évitant les problèmes de décollement du PA-CF des premières couches sur le plateau d’impression, ainsi que d’une buse renforcée, résistante à l’usure provoquée par les matériaux abrasifs comme les composites. Le prétraitement des fichiers 3D a été effectué dans le logiciel BambuStudio, permettant de convertir les modèles en G-code. Concernant les paramètres d’impression, nous avons utilisé une hauteur de couche de 0,12 mm, permettant d’obtenir des surfaces lisses et précises et une vitesse d’impression réduite, optimisée pour un matériau technique, afin d’améliorer l’adhérence entre les couches.
7.2 Prototypage rapide et démarche itérative
Au cours du développement de la douille, nous avons adopté une approche de prototypage rapide en utilisant des impressions 3D en PLA. Ce matériau, à la fois économique et facile à imprimer, nous a permis de valider rapidement les dimensions et les ajustements nécessaires avant de passer à la fabrication finale. L’objectif principal était de définir les jeux optimaux entre les différents composants, notamment entre les mâchoires et la spirale, ainsi qu’entre les mâchoires et la glissière. En général, un jeu d’environ 0,2 mm est suffisant pour des pièces mobiles imprimées en 3D. Cependant, dans ce projet où les composants étaient de petite taille, il a fallu affiner ces valeurs. Cela a nécessité plusieurs itérations pour ajuster et vérifier les tolérances jusqu’à obtenir un réglage optimal. Ces ajustements ont été réalisés en affinant les paramètres d’impression et en modifiant les fichiers CAO en conséquence. Chaque prototype a été évalué sur sa précision dimensionnelle et sa capacité à s’assembler correctement avec les autres pièces. Cette démarche itérative s’est avérée essentielle pour optimiser le fonctionnement de la douille avant de procéder à la fabrication finale dans les matériaux appropriés.

Figure 26 : Démarche itérative
7.3 Assemblage final
Enfin, après l’usinage des différents composants, nous avons procédé à leur assemblage. Les pièces nécessitant une liaison rigide ont été fixées à l'aide d'une colle rapide contenant du cyanoacrylate d’éthyle, un composé actif qui forme un polymère solide lors de la liaison, offrant une excellente adhérence sur le plastique et le métal. L'assemblage a dû être réalisé avec une précision, car il est essentiel pour permettre le bon engrènement des six mâchoires dans la spirale.
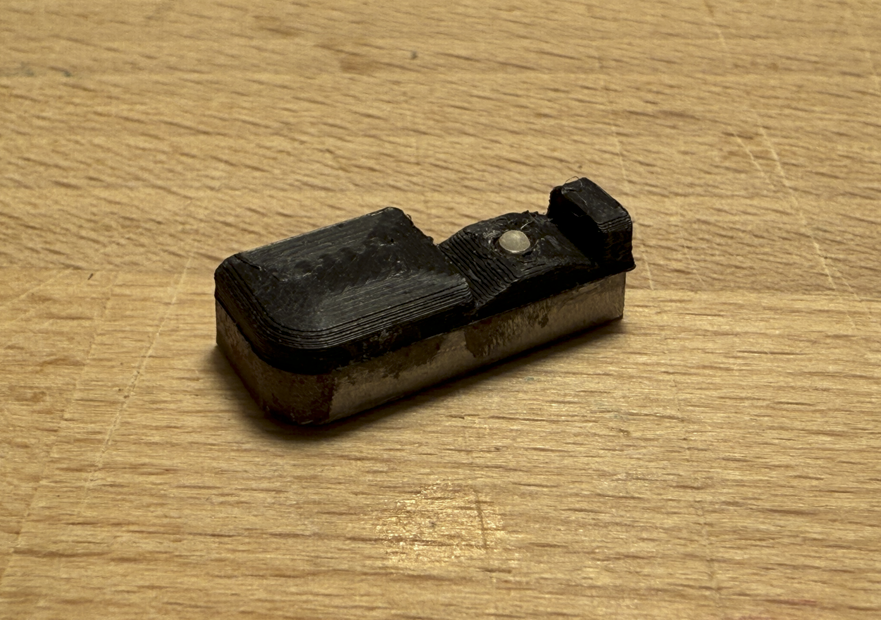
Figure 27 : Mâchoire assemblée en PA-CF et acier S355
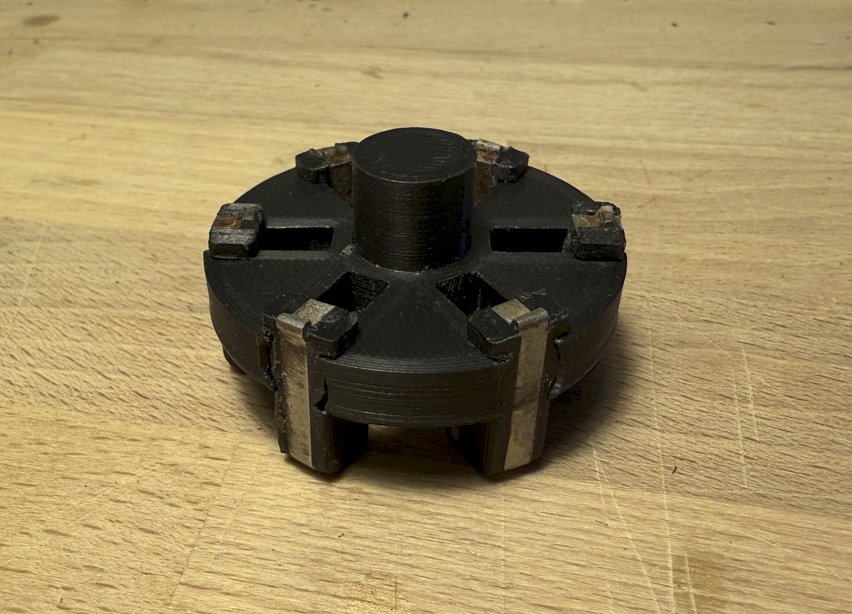
Figure 28 : Assemblage mâchoires et glissière
8. GESTION DU PROJET
Pour être mené à bien, ce projet a nécessité rigueur et organisation. En effet, afin de ne pas perdre de
temps et d’avancer au plus vite et au plus loin, il fallait prévoir les tâches à faire chaque semaine et
suivre les avancées du projet. A chaque séance, nous définissions donc ensemble les tâches les plus importantes
à faire par la suite, et mettions en commun nos divers travaux effectués depuis la semaine précédente. Néanmoins
afin d’être dans les délais et ne pas prendre de trop grandes ambitions, il était également important de prendre
un certain recul pour voir si nos idées étaient réalisables sur le semestre.
Différents outils ont été utilisés pour la logistique du projet. L’outil le plus important fût notre drive
commun pour ce projet.

Figure 29 : Notre Google Drive
Pour tenir clair ce drive et ne pas se perdre dans les fichiers, nous avons également mis en place une nomenclature dans nos noms de fichiers CREO. Cette nomenclature était de la forme :
Par exemple : douille_V1_bati
Chaque mécanisme exploré correspond donc à une version : la V1 est l’idée de Luc avec le système mandrin, la V2, celle de Victor avec la molette et la V3 est celle de Loïc avec la spirale d’entraînement.
Nous avons également tenu à jour un diagramme de Gantt, nécessaire au bon suivi de projet, et permettant de se projeter pour la suite.Pour cela, nous avons configuré une plateforme de gestion de projet, appelée ASANA, qui nous a permis de définir des échéances tout au long du projet pour les différentes tâches, en assignant des responsables à chacune d'elles.

Figure 30 : Diagramme de Gantt
Au niveau du partage de tâches, chacun a apporté au projet ses compétences et ses capacités. Tout d’abord, tous les membres ont contribué à la CAO. Luc possède une imprimante 3D chez lui et un très bon niveau en CAO ce qui nous a permis d’avancer extrêmement vite sur toutes la partie prototypage. Il a également pris le temps d’expliquer ses démarches à Victor et Loïc lorsqu’ils rencontraient des difficultés ou manquaient de connaissances. Ainsi, la CAO a été réalisée de manière collaborative par l'ensemble du groupe, ce qui a rendu essentiel l'utilisation d'une nomenclature claire et d’un serveur partagé pour toutes les pièces CREO. La découpe jet d’eau et les autres machines du FabLab ont été apprises par tout le groupe en même temps. Victor était le responsable du site web et l’a tenu à jour. Enfin, chacun a contribué à la rédaction du rapport.
CONCLUSION
Dans l’ensemble, nous sommes très satisfaits du résultat obtenu avec notre douille ajustable.
Le cahier des charges a été entièrement respecté, et nous avons exploité au mieux les possibilités de
fabrication offertes par le fablab. Bien que les méthodes de fabrication disponibles aient leurs limites,
nous avons maximisé leur potentiel pour atteindre un résultat fonctionnel.
Cela dit, comme tout projet technique, des améliorations restent possibles. Un point spécifique
concerne les ressorts à billes de position, qui n’ont pas réellement apporté de valeur ajoutée. Leur
petite taille ne permet pas de ressentir suffisamment les crans de réglage, ce qui réduit leur utilité dans
le fonctionnement global de la douille. Avec le recul, si nous avions l’occasion de retravailler sur ce
projet, nous chercherions une méthode alternative, par exemple en utilisant des ressorts plus grands
ou en explorant d’autres mécanismes de positionnement pour garantir une meilleure ergonomie et un
retour tactile plus net.
Enfin, ce projet nous a permis de développer de nouvelles compétences, d’affronter des défis
techniques concrets et de renforcer notre capacité à travailler en équipe. À présent, voici les retours
d'expérience individuels de chaque membre de l'équipe.
RETOUR D'EXPÉRIENCE
Loïc :
"Ce premier projet en lien direct avec la spécialité génie mécanique a été très enrichissant pour moi. En effet, en parallèle de nos cours de construction et matériaux qui restent assez théoriques, ce projet m’a permis réellement de « mettre les mains dedans », c’est-à-dire d’appliquer tout ce qui a été vu lors de ces cours et l’importance de cette théorie. J’ai également pu approfondir mes connaissances en CAO et approcher la simulation pour la première fois. Je me suis alors rendu compte que les possibilités offertes par les logiciels de CAO actuels sont énormes, allant de la simple esquisse 2D à une 3D réaliste pouvant simuler des actions réelles. J’ai également approché des machines que je n’avais jamais manipulé auparavant comme la découpeuse jet d’eau ou les imprimantes 3D qui permettent de réaliser des prototypes assez simplement. En bref, ce projet fût un grand épanouissement personnel par la diversité des tâches que l’on a pu effectuer en groupe ! "
Victor :
"De même que Loïc, ce projet fut le premier pour moi dans le domaine du génie mécanique. J’ai tout de suite été captivé par l’idée de réaliser nous-mêmes notre premier prototype et de concevoir quelque chose de concret. En effet, ce projet n’a pas été un simple “cours” comme les autres : il a constitué une mise en pratique des connaissances que nous avons acquises cette année et l’année dernière. De plus, notre choix de projet étant en lien direct avec le domaine de la mécanique ainsi qu’avec notre stage de première année, nous a tous trois entièrement mobilisés et impliqués afin de réaliser la meilleure version finale possible. Par ailleurs, ce projet m’a permis de découvrir l’ensemble des machines mises à disposition au Fab Lab, ce qui m’a permis d’acquérir de nouvelles compétences, notamment en découpe jet d’eau et en impression 3D. Bien sûr, cela m’a aussi appris à maîtriser les logiciels de CAO, grâce à un apprentissage autodidacte ou avec l’aide de mes deux camarades, Luc et Loïc. En somme, ce projet a été très enrichissant pour moi, nous permettant, à nous trois, de progresser dans une excellente ambiance et avec une forte cohésion de groupe."
Luc :
" Au début de ce projet, j'avais déjà une bonne maîtrise de la CAO. Ce projet m'a permis de renforcer mes capacités d'analyse et ma créativité pour répondre à des besoins spécifiques. J'ai apprécié travailler sur ce projet, car l'objectif d'optimisation ou d'innovation par la création d'un produit était pertinent et offrait un large éventail de possibilités. De plus, notre collaboration en équipe a été particulièrement efficace. Travailler en groupe de trois m'a permis d'améliorer mes compétences en gestion de projet et de découvrir de nouveaux outils adaptés. C'était aussi ma première expérience avec des machines comme la découpe jet d'eau, ce qui a introduit de nouvelles contraintes à intégrer dans la conception, notamment au niveau de la géométrie et des matériaux. Globalement, ce projet a été une expérience très positive, me permettant de développer à la fois mes compétences techniques et mes aptitudes au travail collaboratif."
RENDU ET GALERIE D'IMAGES
Voici deux vidéos de présentation et démonstration du fonctionnement de notre Swift Socket.